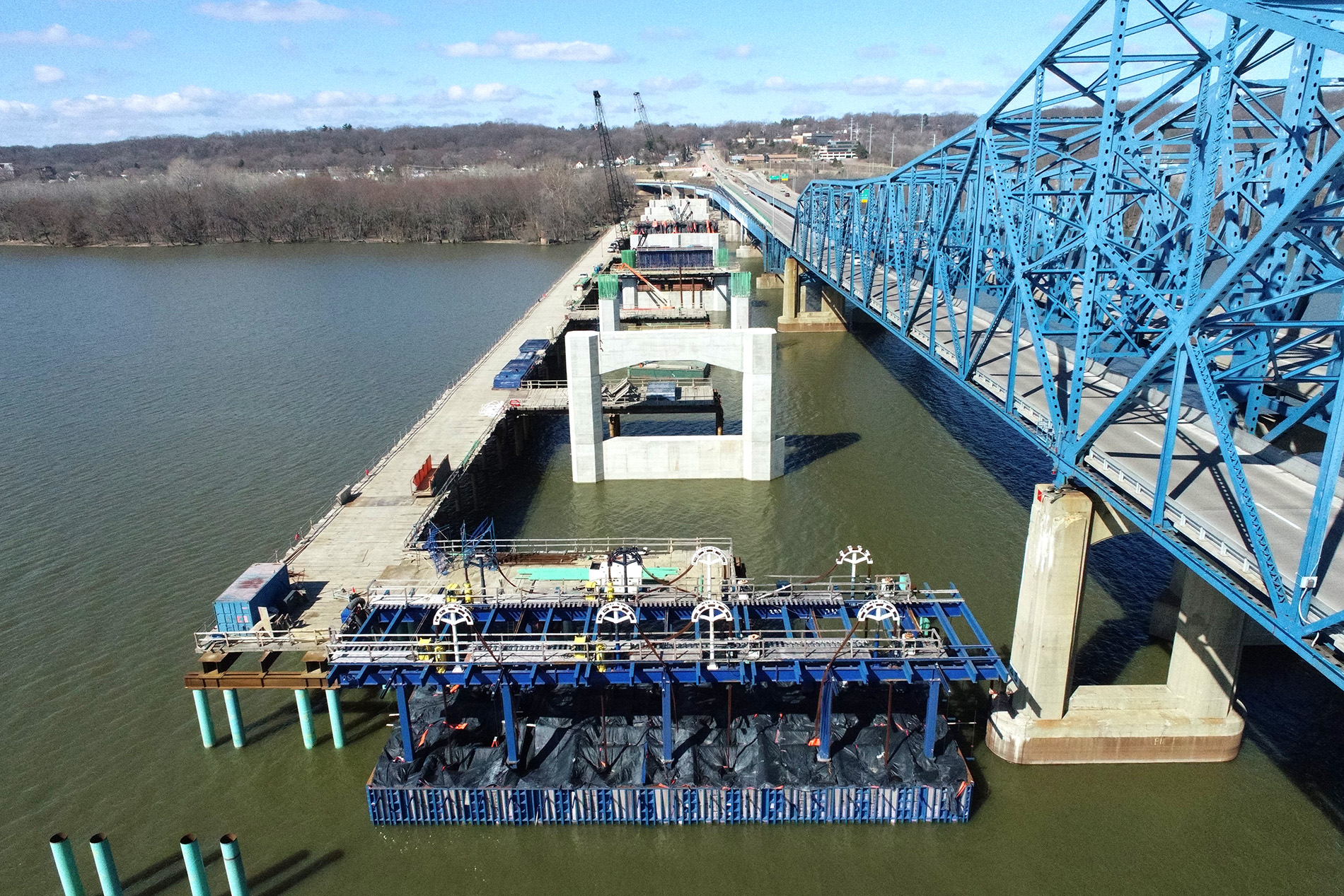
Mike Beres, Director of Operations, Engineered Rigging
In today’s ultra-competitive bidding environment, the selection of equipment for a bridge project is more critical than ever and can be the difference between winning and losing. A healthy mixture of the right equipment and the technical experience to make the equipment do the things required ensures safe and efficient lifting and handling on a project site. Time constraints and site restrictions can create needs for specialty handling equipment in lieu of traditional cranes.
Fueled by the Infrastructure Investment and Jobs Act's (IIJA) $850 billion in funding for civil infrastructure projects, the bridge construction boom is expected to continue in 2024 and beyond. According to Brookings' analysis of White House data, “IIJA implementation is just now hitting its stride…competitive grantmaking is steadily increasing, with 80% of all competitive funding still left to be awarded.” A number of states and local governments are expected to leverage the federal dollars for bridge and overpass work in the coming years.
By leveraging innovative equipment, civil contractors and Department of Transportation leaders can optimize safety, control costs and minimize traffic interruptions. In this article, we explore a collection of heavy lifting and specialized transport equipment ideal for bridge construction, repair and demolition projects.
Crane-Free Solutions for Bridge Construction
For new bridge construction, incremental bridge launching delivers a crane alternative. Popular in Europe and gaining more consideration in the Americas, this approach is extremely effective when constructing very high bridges. The bridge segments are built on the bridge approach in a launching bay and moved into position using equipment such as hydraulic strand jacks and Hilman rollers. Incremental bridge launching was employed to build the tallest bridge in Kentucky, the Pond Creek Bridge. Bridge launching jobs require planning to ensure the structure is suited for sliding.
“The unique ability of a strand jack to lift or pull a load over long distances makes it an ideal bridge construction solution. Our rental fleet of strand jacks is scalable by design, and we are able to accommodate changes in both capacity and length of pull requirements by using this proven technology,” explained Christopher Cox, PE, Founder and President of Engineered Rigging.
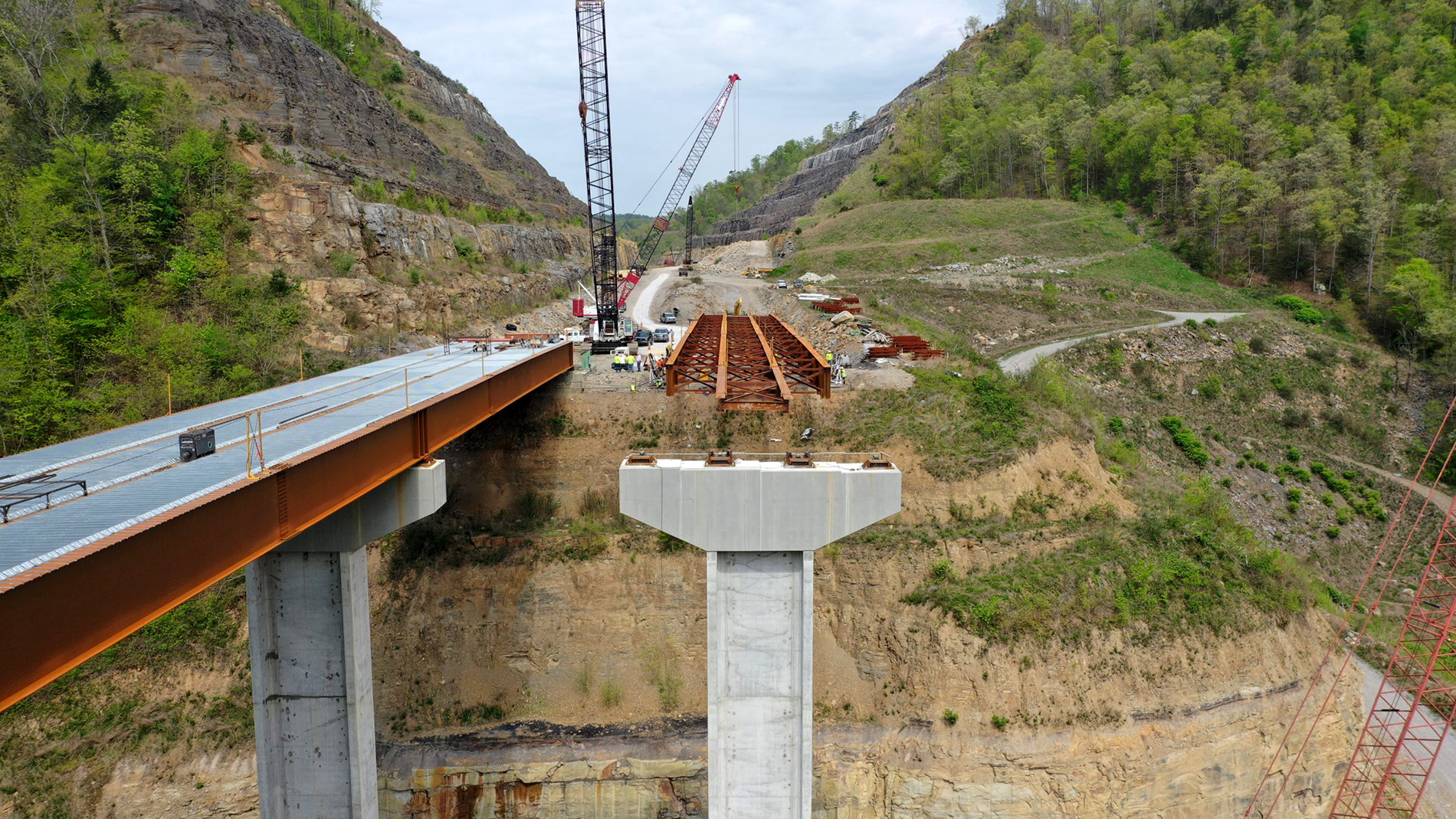
Rapid Bridge Repair & Replacement
Restricted site conditions for either space or outage conditions may dictate building a bridge span off-site and rapidly replacing it during a short outage window such as a night or weekend closure. In such cases, it may require transporting a bridge into position and lifting it into place onto bearings at abutments or pier caps. In combination with a system of Goldhofer Self-Propelled Modular Transporters (SPMTs), the Enerpac JS-500 Jack-Up System provides precise control and a proven strategy to lift and install a bridge span.
When the completed bridge is ready for transport, the SPMT/JS-500 system moves into place under the bridge and takes the load. After it is secured, the SPMT maneuvers the load into place at a relatively low riding height. Once adjacent to the installation location, the JS500 system goes to work. As the JS-500 legs lift the load, barrels are added to the legs of the jack-up system to incrementally achieve the desired height. The system, featuring synchronization of multiple networked lift points, provides a safe and precise lift. Once the bridge span is at the required height, the JS-500 mechanically holds it in place while it is secured. Once the bridge span is secured, the SPMTs move the load to final alignment and the JS-500 system is again employed to lower the load. View the Video
The JS-500 has a 2,200-ton lifting capacity to heights up to 50 feet. Precision control is achieved while maintaining an average lifting speed of approximately six barrels or 14 feet per hour. The modular design offers flexibility, simple mobilization to site, and expedited setup and teardown which accelerates the replacement of a bridge section. Another key feature is its compact footprint compared to conventional cranes.
The Bridge Bearing Replacement Kit provides a safe way to expedite a common bridge maintenance activity, bridge bearing replacement.
“It’s important to be able to lift a bridge safely and evenly during these routine activities to ensure bridge integrity is maintained. Bridge owners don’t want to hear that their bridge concrete was cracked or damaged during a lift,” noted Cox.
A typical kit includes a hydraulic pump, such as a split flow pump, which equally distributes oil to downstream cylinders. The cylinders, often locking collar cylinders, either low height or standard height, lift the bridge hydraulically and when in position are locked by spinning a collar in place to mechanically support the bridge while the bridge bearing work is conducted. When required, the kit’s added computer synchronous control can deliver lifting precision to accuracies of 0.040” between leading and lagging cylinder. Synchronous lifting and mechanical locking make for safe and predictable maintenance operations.
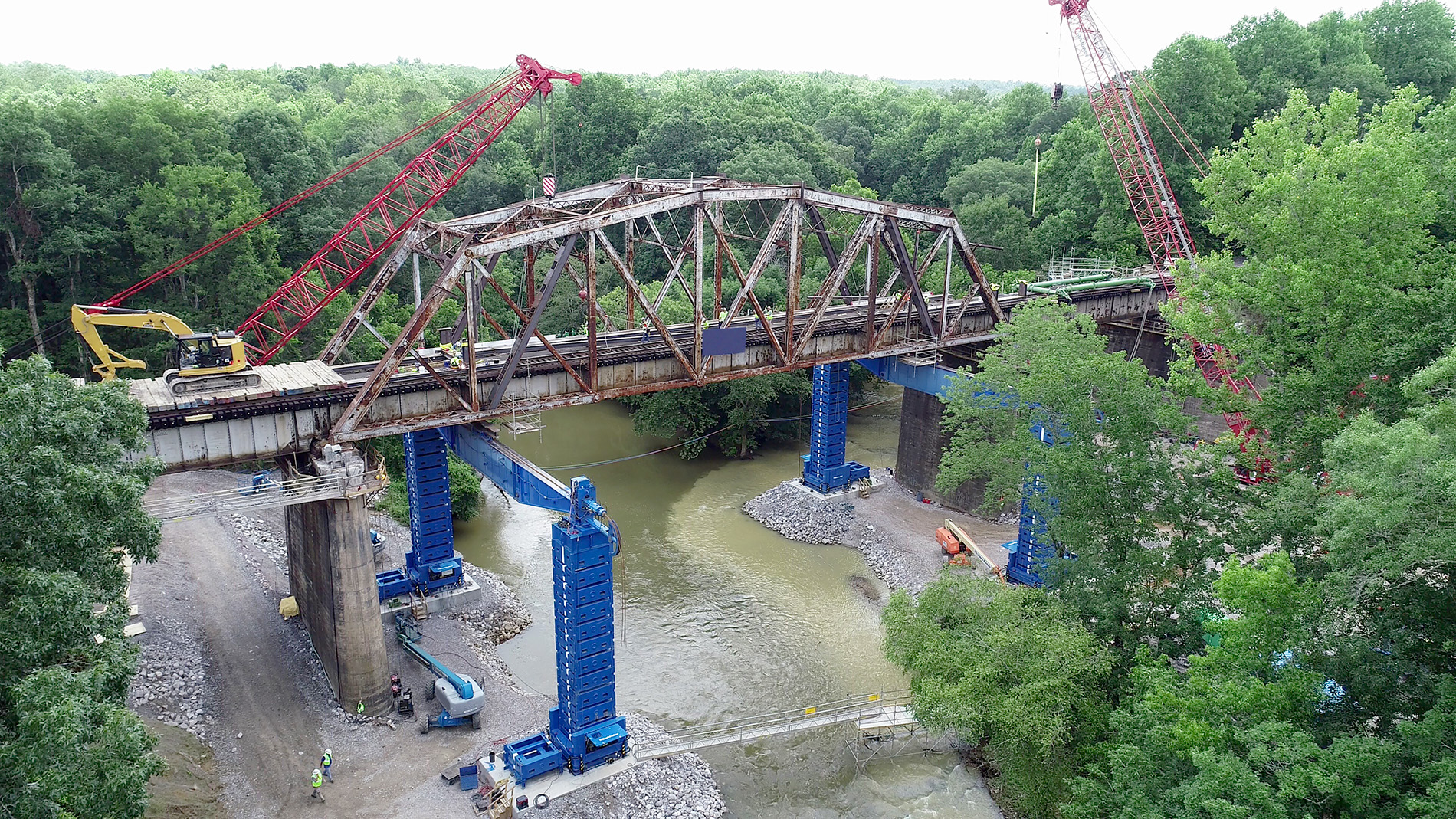
Expedited Bridge Demolition
Many of the aging bridges in the United States are beyond repair and will need to be demolished. Once again, innovative equipment can save time and optimize safety. The dismantling of the 90-year-old Wittpenn Bridge in New Jersey offers a prime example. The deteriorated condition of the bridge prevented a “grab and lower” approach. Instead, a strand jack system was used to precisely control the lowering of three sections of the bridge: two counterweights weighing nearly 450 tons each and a 209-foot-long vertical lift span weighing nearly 900 tons. View the Video
The aforementioned JS-500 Jack-Up System can also be deployed to lower spans of a bridge during demolition.
By combining bridge expertise with a thorough understanding of innovative heavy lifting and transport technologies, Engineered Rigging is able to solve the unique challenges of bridge projects. All of the technologies featured in this article are available to rent or buy. Please contact sales@engineeredrigging.com or call 1-844-474-4448 to discuss your project.
